Toner
DYMO – Think Again
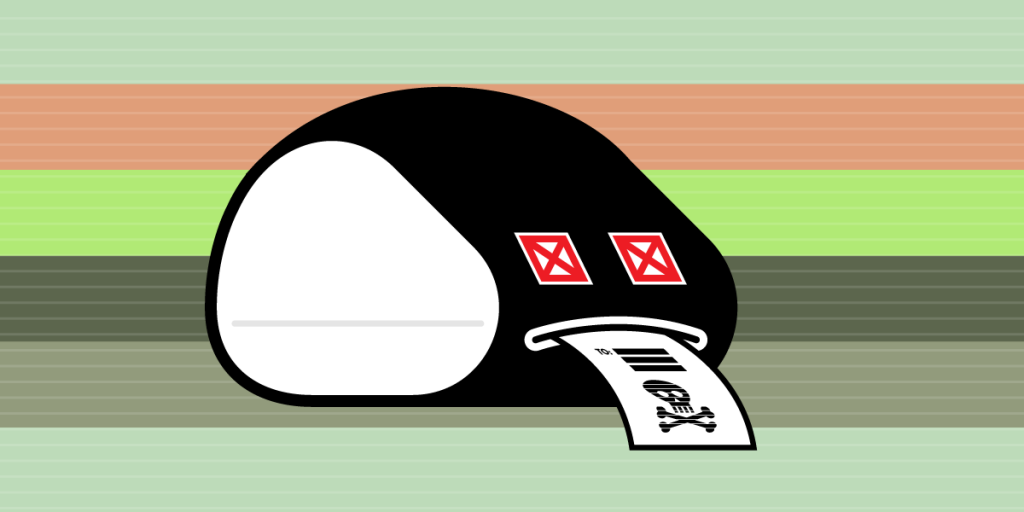
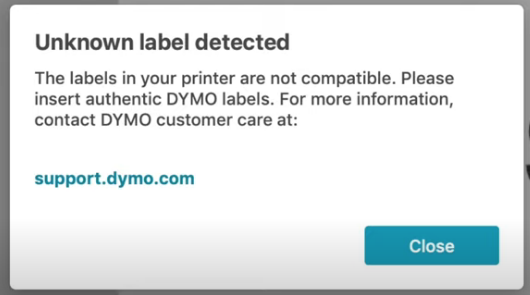
Are you well organized? Do you have a garage full of well-labeled bins or a pantry full of neatly labeled jars? Do you ship a lot of stuff and print labels?
If so, you probably own and cherish your label maker. What’s not to like? Well, if you’re a Dymo label maker owner, there’s a new scam that might convince you to switch brands – if it doesn’t scare you off labels altogether, that is.
For a certain kind of corporate executive, the printer business is a source of endless temptation. After all, printers go through lots of “consumables.” That means that printer manufacturers don’t just get to sell you a printer, they also have a chance to sell you ink, forever. There’s nothing wrong with this business. In theory. In practice, though, printer companies are greedy. They’re not content to be one of many companies offering ink in a competitive market. Rather, they want to be your only ink supplier, and boy oh boy do they want to charge you a lot of money for it – up to $4,000 per litre! No one would voluntarily pay $4,000/litre for ink that costs about $50/litre to manufacture, so the printer companies roll out an endlessly inventive bag of dirty tricks to force you to buy their $4,000/litre product, and keep you buying it, forever.
Now, printers have two consumables, ink and paper, but all the manufacturers’ effort is focused on the ink side. That’s because ink comes in cartridges, and printer companies can add cheap chips to their cartridges; the printer can send these chips to cryptographic challenges that require secret keys held only by the manufacturer. Other manufacturers don’t have the keys, so they can’t make a cartridge that the printer will recognize and accept. This strategy is lucrative but it has its limits: it falls to pieces the minute there’s a supply chain problem that means printer manufacturers can’t get chips anymore! The pandemic was hard on a lot of companies, but it was a boom-time for the delivery industry and the firms that supply it. The desktop label maker sector thrived during the lockdown, as hundreds of millions of people switched from shopping in person to buying things online – things that were delivered in boxes bearing barcode labels printed on a desktop label-printer. Label printers are thermal printers, which means that they don’t use ink: instead, the “print-head” consists of tiny electrical elements that heat up special, thermoreactive paper that turns black when it is heated. Lacking ink, the label-printing market has been spared the kinds of shenanigans that plague the world of inkjets…until now.
Dymo is a household name: founded in 1958 with a breakthrough gadget that embossed capital letters onto rows of adhesive-backed tape, the company is now a division of Newell Brands, a giant, many-headed corporate hydra whose other companies include Rubbermaid, Mr. Coffee, Oster, Crock-Pot, Yankee Candle, Coleman, Elmer’s, Liquid Paper, Parker, Paper Mate, Sharpie, Waterman, X-Acto and many, many more. For all that Dymo is part of this corporate empire, it has not heretofore been able to avail itself of the tricks that created approx $4,000/litre printer ink.
That’s because the only consumable that Dymo owners need is labels, and labels are a standardized product, with many, many vendors producing them and selling them for use with many, many different brands of label maker. Some people might be willing to pay a little extra for Dymo’s own label-rolls, but if not, there are plenty of other options: not just cheaper labels, but labels designed for other uses, with different adhesives and finishes. Those people are going to be disappointed.
Dymo’s latest generation of desktop label printers use RFID chips to authenticate the labels that Dymo’s customers put in their printers. This lets Dymo’s products distinguish between Dymo’s official labels and third-party consumables. That way, the printers can force their owners to conduct themselves in the ways that serve the interests of Dymo’s corporate owners – even when that is to the owners’ own detriment. There is no (good) reason for this. In its sales literature, Dymo extols the virtues of chipping its label-rolls: auto-sensing of label types and auto-counting of remaining labels – and they boast that “[t]he direct thermal printer replaces the need to buy costly ink or toner.” But what they don’t say is that this printer forces you to buy Dymo’s own labels, which are substantially more expensive than many of its competitors’ labels (Dymo’s labels retail for about $35-$100 per roll; alternatives, about $10-$20 per roll). The reason they don’t say this is obvious: no one wants this. If a Dymo owner wants to buy Dymo labels, they will buy them. The only reason to add this anti-feature is to force Dymo owners who don’t want to buy Dymo labels to buy them anyway.
All the advanced features that Dymo touts for its RFID-locked labels could be attained without the lock-in. For years, Dymo owners have assumed that they can use any labels with their printers. While some third party retailers have added warnings about this label lock-in, the biggest retailers haven’t followed suit – instead, their customers are warning each other about the bait-and-switch.
From the online reaction, it’s clear that Dymo’s customers are pissed.
Some are congregating in technical discussions of how the measure might be defeated, but so far, no vendor has stepped in to offer a jailbreaking tool to let you modify your label maker to serve your interests, not Dymo’s shareholders. There’s a good reason for that: U.S. Copyright law gives Dymo a powerful tool to intimidate commercial rivals who help us escape from label-jail. Section 1201 of the Digital Millennium Copyright Act exposes those rivals to US$500,000 in fines and a five-year prison sentence for trafficking in tools that bypass an “access control” for a copyrighted work, like the firmware on a Dymo printer.
While it’s not clear that a judge would rule in Dymo’s favour, very few commercial operators are willing to take the risk when the stakes are that high. That’s why we’re suing to overturn Section 1201. The law moves slowly, and bad ideas can travel around an industry like a virus. So far, Dymo’s alone in putting DRM in paper. Its rivals, like Zebra and MF Label, still make printers that let you decide whose labels you want to buy. These printers aren’t cheap – $250-$400 – but they’re also not so expensive that they constitute the majority of the operating costs of owning one. Over the life of one of these printers, you can expect to spend far more on labels than on your printer. That means that the smart move for a Dymo 550 and (Dymo 5XL) owner is to throw it away and buy a competing model from a competitor. Even after you eat the cost of your Dymo product, you’ll still save money in the long run. Dymo is trying something unprecedented here. DRM in paper is such an abysmal, abusive idea that we should all recoil from it.
Dymo’s betting that people who get suckered into buying its latest models will shrug and take it. But we don’t have to do that. Dymo has lots of competition, and it is vulnerable to bad publicity. This is one of those rare moments where a terrible plan is being hatched and we have the chance to stake it through the heart before it can reproduce.
BY CORY DOCTOROW FEBRUARY 15, 2022
What Happens To your Printer if You Cancel Your HP Instant-Ink Subscription?
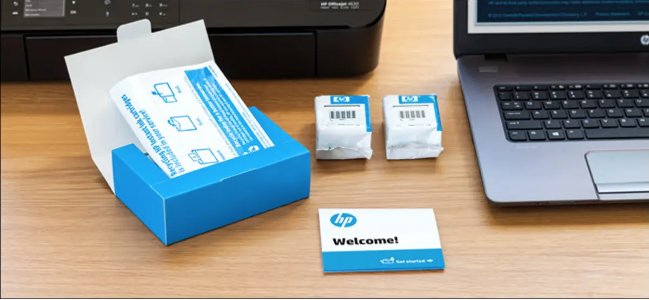
HP’s Ink Subscription Has DRM That Disables Your Printer Cartridges
HP have recently introduced this selling subscription consumables in Australia
The below article posted by Josh Hederikson (Catteriain) Sept 16th 2019 and refers to his experience with the USA subscription service.
Printer ink is expensive. HP promises to help with a subscription service for ink, complete with cartridges that stop working when you cancel your subscription. But HP makes you count pages, and I’d rather print as much as I want.
HP’s Ink Subscription Service Sounded Like a Good Deal
In mid-2016 I was running into a recurring issue. I was always out of printer ink, and new cartridges were expensive. Laser printers can be cheaper for many people, but my household does print as many color photos as it does text documents, which means they’re not a good choice for me. So I purchased a new inkjet printer on the promise of HP’s easy-to-use ink subscription service. For a low cost, I would always have all the ink I needed—as long as I kept to a page limit, that is.
Now, years later, I’ve realized there was one other price of admission. The ink they’ve sent me isn’t mine; it’s theirs. And if I cancel the subscription when the billing cycle ends, the printer won’t use the ink anymore, and HP requires I send it back to them. I have to buy new ink to replace the ink that is already in my house.
HP Instant Ink is Easy to Use, and Inexpensive Up Front
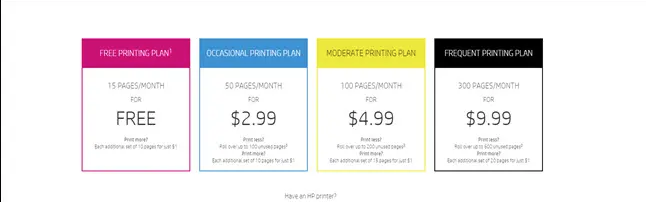
Note- USA pricing
HP
As long as your HP internet-connected printer supports it, HP Instant Ink is very easy to set up. You go to their enrollment site, sign up for an account, and connect your printer. Once you finish signing up, HP will send you ink cartridges; billing begins when you install them in your printer. HP requires you to choose a plan that limits the pages you can print each month. HP doesn’t care what you print, just the pages needed for the job. A page with a single word on it and a full-colour photo page are both the same as far as the plan is concerned. If you don’t use all your allotted pages in the month, the extra pages roll-over and you can use them next month.
How much you pay depends on the number of pages you can print and roll-over. HP offers a free plan with 15 pages per month, but no roll-over. If you go over the limit, you pay $1 for each set of 10 pages you print (meaning if you print five pages, you still pay $1). The first paid tier is $2.99 a month for 50 pages, and the ability to roll-over 100 pages from previous months. Additional pages are still $1 for a set of 10 pages. The next step up is $3.99 a month, with 100 pages per month and 200 roll-over pages. You’ll pay $1 for sets of 15 pages if you go over at this level. The top tier is $9.99 a month at 300 pages, and 600 roll-over pages. You’ll pay $1 per 20-page set if you go over this tier limit.
The Ink Stops Working if You Cancel
Here’s the kicker: if you cancel, your ink stops working. You read that right; as soon as your billing cycle ends the printer will not accept the ink anymore, and you’re required to send it back to HP. At least they provide the postage and packaging for that purpose.
HP doesn’t spell out any consequences in their terms of service for failure to send the ink back, so we checked with a support agent. They helpfully explained that nothing happens if you fail to send them back, but the cartridges would stop working. You’ll have to buy more ink on your own if you want to keep printing. HP ships specially marked ink as part of this process, and your printer recognizes that it is intended for Instant Ink subscribers only. It’s essentially DRM, but instead of locking down a digital movie or book, this locks down a physical product: the ink in your printer.
Instant Ink requires an internet connection for your printer. HP explains that they monitor your ink levels, so they know when to send you more, but as described in their Terms of Service the other reason for this is to remotely disable your ink cartridges if you cancel, or if there are any issues with your payment.
Those terms also give HP permission to “remotely change, patch, update, or otherwise modify your printer’s software, firmware or programming, without notice to you” to provide the Instant Ink service. HP also says it will remotely monitor your printer’s page count and ink status, as well as the “types of documents printed (e.g., Word, PowerPoint, pdf, jpeg, etc.).”
You’ll Save Money if You Print Mostly Colour
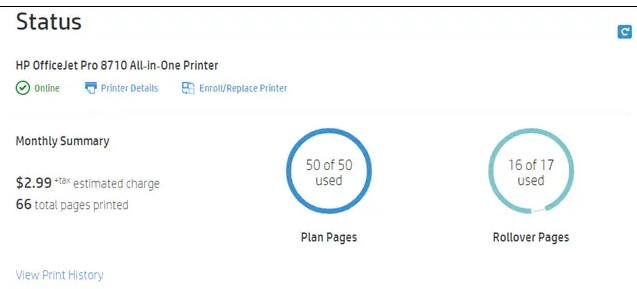
If you’re asking whether HP instant ink is a good deal, the answer is a resounding: it depends.
In a little over two and a half years, I’ve printed 1517 pages. Many of these are full-color prints for photos, labels, and so on. But this has also included a mix of regular black and white documents, too. Thanks to roll-over pages I have avoided extra charges every month except four. Three out of those four months, I printed less than ten over the limit pages; one month I printed an additional 116 pages. So while most months I paid $3 to $4, one month I paid $16 for my excessive page prints
Overall since I joined HP ink I’ve spent just under $110. Comparing that to the cost of ink, I’m doing well. Since I signed up for the program, HP shipped one black cartridge and two of each color cartridges. I’m currently sitting at less than 25% in the existing black cartridge and about 50% of the color cartridges. The exact ink HP sends isn’t for sale, but they describe it as ‘extra high capacity‘ in their FAQ. The closest equivalent I can find for my printer is High Yield cartridges. They sell a full pack (black, cyan, magenta, and yellow) for $110, and a color pack for $66. So side by side, I’ve received $176 worth of ink and only paid $110. You could try to save money with third-party cartridges, but HP and other printer manufacturers have a long history of fighting their use. And HP’s legal text include lines that explain using a third-party cartridge will void the warranty.
While the pricing math is working out well for me, it may not work as well for you. HP only sends ink when you need it, so if you print far less or far more than I do, or you print just text documents, then the math changes. It’s easy to get trapped into overages, and while you can step up or down in your plan to avoid that, you have to pay attention to know when it’s necessary.
The only way to know how many pages you’ve printed is to log into HP’s website and check first. If you forget to do that and don’t keep track, you can go way over your plan. HP won’t automatically move you up to the next level either. That’s what happened to me in November: I went 100 pages over my limit and didn’t notice until the bill arrived. By that point, it was too late to step up to the next level, which would have saved me money.
Worse yet, if you need to replace your printer, you have to do it through HP, or you will lose your roll-over pages and plans. Every time I print, the first page is a blurry mess (which counts against my limit). But, unless I want to lose the ink I paid for, I have to use the “Replace a Printer” process on HP’s website.
I’m Tired of Being Afraid to Print
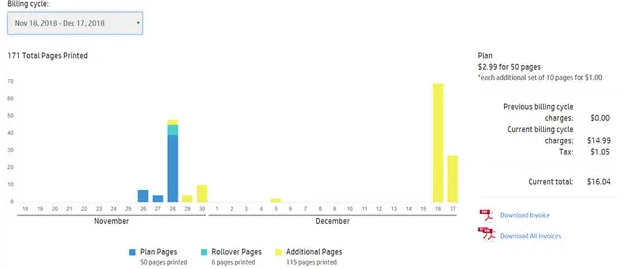
HP Instant Ink is designed and billed as a ‘set it and forget it’ service, and while that does add to the convenience factor of everything, it’s also the trap. And it’s why I want to quit.
According to the math, I’m the type of person who can benefit the most from HP’s Instant Ink program. I’m getting more ink for less money than if I had gone a traditional route. But there’s a secondary cost. I’m left afraid to use my printer for the one reason I have it—printing. It’s a strange proposition that every time I go to print, I now feel the need first to check if I have enough pages left in my plan. It’s like asking HP for permission to use my printer. And if I don’t ask nicely enough, I’ll pay extra or, worse, they’ll take my ink away. And it’s not actually my ink: HP’s instant ink recycling page spell this out clearly (emphasis mine):
HP Instant Ink cartridges are the property of HP and must be returned when empty, or when your service is cancelled
I can’t think of anything else in my house that works this way. My couches don’t have an allotment for sitting time, and I don’t need to continually pay the furniture store a fee for the right to use their cushions. I don’t fear that if I fail to pay my cushion subscription the store will take them away, leaving me with a cushionless couch.
My laundry machine requires detergent, but I’m not limited in the number of loads I can wash in the month. I don’t pay extra for doing the laundry more often when it happens to be rainy and muddy, and beyond keeping my detergent stocked, I’ve never felt need to check if it’s okay to wash my clothes. If I decide I don’t like the brand of detergent I’m using today, I’m not required to send it back just because I’d like to change.
But that how it feels with my printer. I don’t want to stop what I’m doing, go to a website, and check if I’m allowed to print. I want my printer to be mine and controlled by me. All I have to do is convince myself that freedom is worth the cost of all new ink.
Fuji Xerox taken to court over alleged unfair contract terms
Automatic renewal terms, excessive exit fees and unilateral price increases are just a few of the unfair terms – Julia Talevski (ARN)22 October, 2020
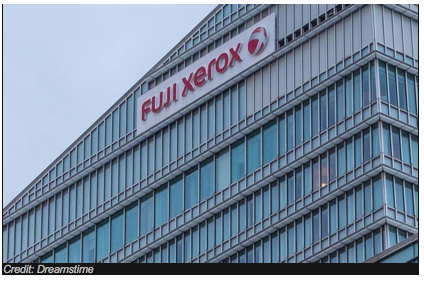
Automatic renewal terms, excessive exit fees and unilateral price increases are just a few of the 31 different ‘unfair’ terms the Australian Competition and Consumer Commission (ACCC) has picked up on among its allegations involving nine types of Fuji Xerox’s standard form small business contracts it claims contain 173 unfair contract terms.
“We have received a number of complaints from small businesses alleging that some of the terms in Fuji’s contracts have caused them significant financial harm,” ACCC deputy chair Mick Keogh said.
“Some of the unilateral variation terms allow Fuji to modify contracts by creating new rights and obligations, including increasing prices, without notifying its customers and without giving them any corresponding right to negotiate or reject.”
According to the watchdog, the terms were used in contracts between Fuji and its small business customers for the supply of printing goods, services and technical assistance since at least October 2018.
The ACCC will argue that the unfair terms in these contracts cause a significant imbalance in the rights and obligations of Fuji and the small businesses they contract with,” he said.
The ACCC is seeking declarations that the terms in the existing contracts between Fuji and its small business customers are unfair and therefore void, and an injunction to prevent Fuji from relying on these terms in its current contracts or entering into future contracts that contain those terms.
The ACCC is also seeking an order for a corrective notice, a compliance program and costs.
Keogh sounded a warning this court action should prompt all other traders in the printing support industry to review their standard form contracts and make any necessary changes to remove unfair contract terms.
Fuji Xerox (FXA) said it had been cooperating with the ACCC’s investigation and had proposed several contract changes to address the contract concerns.
“In that context, FXA is disappointed that the ACCC has decided to commence proceedings, which FXA intends to defend,” FXA said. “FXA is sending correspondence to all its customers about how this impacts them and next steps.”
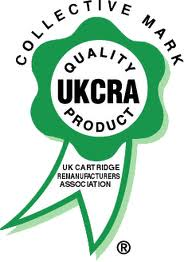
HP has given assurances to the United Kingdom’s Advertising Standards Authority that they will remove the claims from their future advertising.
In its email, HP claimed that “over 1 in 5 problems caused by non-HP cartridges can cause damage to the printer” and that “49% of imitation cartridges failed during use or right out of the box”, compared to HP original supplies.
With the complaint UKCRA asked the ASA “to request HP to cease and desist from any further campaigns of this sort” stating that the advertisement includes “many statements that are discriminatory” and tries to “to discredit third party toner and inkjet printer cartridges other than their own in their printers.”
UKCRA added at the time: “Printer cartridges that are remanufactured (re-used) are not only more environmentally friendly they are more sustainable than recycling.”
The ASA has now received an answer from HP, who have assured the authority that they will remove the claims from their future advertising.
A check of the HP site reveals that the email in question either does not exist anymore on the server, or it may have been moved or deleted.
ASA said in its message to UKCRA: “We consider that this will resolve the complaint without referring the matter to the ASA Council, and will consequently be closing our file.
“In a formal investigation, if the ASA Council decides that an ad is in breach of the Code, the advertisers are told to withdraw or amend it. Because HP has already assured us that the advertising you complained about will be amended, we consider there is little to be gained from continuing with a formal investigation, which would achieve that same outcome.”
Although ASA is not publishing full details of the UKCRA complaint on its website, www.asa.org.uk, basic information including the advertisers’ name and where the ad appeared will appear though on 9 September 2020.
We note as we publish this article HP in Australia have not removed from local site
Compatible vs Genuine
Will compatible Toner & Ink cartridges work as well as the genuine?
Yes…. Compatible Toner & Ink manufacturers have developed their own solutions that work just as well as genuine product – ie: Original Equipment Manufacturer (OEM).
They have had the opportunity to reverse engineer the OEM product allowing them to develop outstanding ink and toner solutions to ensure the quality of the finished printed page is of the same quality you are familiar with.
People have embraced non genuine ink & toner cartridges.
Why? Because they come with a guarantee to deliver the same quality as the OEM products, but at a fraction of the price.
Don’t be bullied by OEM printer manufacturers
If you do you will lose the opportunity to make significant savings. In today’s competitive marketplace, printer manufacturers often use scare tactics to maintain their unrealistic profit margins, such as claiming the use of non genuine toner and inkjet cartridges will void manufacturers warranty.
This is simply not true, just like vehicle manufacturers cannot cancel your warranty because your chose a competitor to service your vehicle, you have the right of choice for your home or office equipment.
Schedule 2 Part 3-2 of the Competition & Consumer Act 2010
“If a part is ‘non- genuine’ but is interchangeable with a ‘genuine-part’ then the non-genuine part would still be seen as fit for purpose, and therefore would therefore not void any manufacturers guarantee/warranty. Such warranty can only be voided when the cartridge itself is faulty and causes damage to the printer.”
With the latest technology and a superior quality of print solutions, colour and mono copier toners have been tried and proven worldwide.
Why do compatibles sometimes look different, yet work the same?
Patents protect most OEM printers and cartridges, so manufacturers of compatible cartridges may be required to redesign their products to avoid intellectual property infringement.
This allows the compatible manufacturers to make any improvements necessary to the original design in order to deliver optimal cartridge performance. So, although compatibles may look different to the original product the quality and suitability is assured.
These cartridges are brand new and not re-manufactured.
If a cartridge shell cannot be redesigned, due to patent restrictions, the original cartridge may be refilled, with any used component replaced.
In summary
The choice is yours – if you are looking for toner or ink that is considerably more affordable than the Original equipment manufacturer – then give the compatibles a try
get savvy and calculate the true cost per print – simply take the cost and divide by the yield
example
Brother TN2350 toner cartridge – Genuine $134.95 average yield 2,600 pages . = .0519 cost per print
Brother Tn2350 toner cartridge – Compatible $57.95 average yield 2,600 pages =.0222 cost per print
At CartridgeMate we provide full warranty as well as technical support for all genuine and non- genuine print toner manufacturers
Does your HP printer not let you use other cartridges? You could be compensated.
Below is email received from the ACCC on 4th May 2018 with respect to Hewlett Packard admitting that it designed technology to prevent non genuine cartridges being used – and in many cases, customers received a error message which indicated the cartridge was damaged . – when this was not the case
We sell Genuine as well as Non- Genuine cartridges for most printer brands – as we believe that the customer should have a choice.
Some OEM ( Original EquipManufacturers) should you have a issue, will immediately state that because you are using a non genuine cartridge that the warranty is void. This is untrue – they have to prove that the cartridge damaged the printer. This simply appears to be a way for OEM to keep customers purchasing their product and limiting the end users choice.
If you purchased certain models of HP printers and weren’t informed that non-HP ink cartridges might be incompatible – you could be eligible for compensation.
HP has given the ACCC a court-enforceable undertaking after it admitted to not disclosing to its customers that certain printers, or their firmware updates, included technology that was designed to prevent non-HP ink cartridges from being used. This resulted in non-HP ink cartridges being rejected, and in many cases, customers receiving an error message which indicated that the cartridge was damaged, when this was not the case.
HP will compensate $50 to its customers who were prevented from using a non-HP cartridge. If you believe your business is entitled to claim compensation, visit the HP website.
Find out more, including the printer models affected, in our media release.
Lesson for businesses: This matter serves as a timely reminder to businesses that you must disclose all important information about your products, including if there are any restrictions on the use of non-genuine parts. If businesses fail to provide relevant information to consumers about their products they could be breaching the Australian Consumer Law by engaging in false, misleading or deceptive conduct. You can find out more about advertising and promoting your business in our recently updated Small business & the Competition and Consumer Act guide.
Kind regards,
Small Business team
Australian Competition and Consumer Commission (ACCC)
Safely Storing Ink Cartridges For Maximum Performance
There’s nothing worse than coming to print and finding that the ink cartridges you purchased a while ago no longer work.
Storing ink cartridges properly can lengthen their life span dramatically. With just a few tips on how to store your ink cartridges, you can make sure that your ink lasts until required.
1.) Store in Upright Position Whether it is in its box or loose, make sure to stand the ink cartridge in an upright position at all times. We recommend keeping cartridges with the print head facing up, especially cartridges that contain more than one colour. Storing cartridges lying down could cause inks to mix.
2.) Keep in Cool Conditions Store all ink cartridges in a cool ventilated place (15° to 35° Degrees) and do not expose to temperatures over room temperature. Ink could start to foam up creating bubbles which can cause leaks or air locks.
3.) Keep the Cartridge Sealed This keeps the ink in its original state keeping the print head moist. No air escapes or gets caught in the cartridge, ensuring to keep any chemical reactions kept to a minimum.
4.) Seal the Cartridge Bag Moisture is important when storing ink cartridges, so seal the bag with the cartridge inside. If the bag has been opened, try sealing the bag with sticky tape.
4.) Keep in a Dark Room Keeping the cartridges in a dark room stops the ink quality being degraded by direct sunlight. Ink cartridges that have already been opened can be stored for up to 6 months if kept in the right conditions, whilst new and sealed cartridges can last for 2 years.
If cartridges have been stored for a while and you wish to print, do not just insert the cartridge into the printer and begin printing. Doing this could damage your printer and waste your ink.
Just follow these quick steps:
- Unseal the cartridge, check for any ink spills and wipe any dust and spills
- Check the print head is moist by wiping tissue paper across the print head.
- Make sure the cartridge contact terminals appear as they should be.
- Insert into printer and print a test page.
How To Store Toner Cartridges
Toner cartridges contain components that are sensitive to light, temperature and humidity.
These recommendations should help ensure optimal performance, highest quality, and longest life from your Original or new compatible cartridge.
Store cartridge in the same environment in which the printer will be used. This should be in controlled temperature and humidity conditions.
The Original or compatible cartridge should remain in its original and unopened package until installation – if original packaging is not available, cover the top opening of the cartridge with paper and store in a dark cabinet.
Opening the cartridge package prior to use dramatically shortens its useful shelf and operating life. Do not store on the floor. If the toner cartridge is removed from the printer, follow the instructions below to store the toner cartridge properly.
- Store the cartridge inside the protective original packaging.
- Store lying flat (not standing on end) with the same side facing up as if it were installed in the machine.
- Do not store consumables in any of the following conditions:
o Temperature greater than 40°C.
o Humidity range less than 20% or greater than 80%.
o An environment with extreme changes in humidity or temperature.
o Direct sunlight or room light.
o Dusty places.
o A car for a long period of time.
o An environment where corrosive gases are present.
o An environment with salty air.
Handling Instructions
- Do not touch the surface of the photoconductive drum in the cartridge.
- Do not expose the cartridge to unnecessary vibrations or shock.
- Never manually rotate the drum, especially in the reverse direction; this can cause internal damage and toner spillage.
Common Cartridge Failures
OPC Drum Failure
The most common cartridge failure is predominantly due to the drum. The drum has the wiper blade scraping any excess toner off the surface as well as the paper or Transfer Belt rubbing against it as it prints. Common OPC drum failures are:
Perfectly straight and very thin vertical line running full length of page:
Indicates a scratched/ringed drum generally from foreign matter or build up of toner on the Wiper Blade, which scratches/rings the Drum during rotation.
Dots that repeat equidistance down the page:
Indicates a chip in the drum surface, referred to commonly as a “pinhole”. The distance between the dots is dependent on the circumference of the drum (generally 4 times). Some pinholes, on closer inspection, can be built up foreign matter which can be removed/cleaned with a cotton tip and Iso-Propyl alcohol.
Dots that repeat equidistance down the page, some are accompanied with a full horizontal band across the page:
The dots indicate a pinhole and the band across the page. Indicates a short/spike against the PCR, which is due to the pinhole.
Smears of toner across (horizontal) page and are equidistance apart (vertical):
Caused by light damaged drum coating (sunlight). The distance between the smears is dependent on the circumference of the drum, generally 4 times. Exposing the Drum to direct light for long periods of time damages the coating/film.
Full thin line across the page, equal distance apart:
Calculate the circumference of the drum and if the thin lines are the same distance apart as the Drums circumference then the Wiper Blade has marked the Drums coating. This generally occurs with periods of time where the WB rests against the drum (storage). Heat can play a role in this.
Grey “tyre tracks” on right or left side of page:
This failure is also sometimes described as wind blown sand. It is caused by a worn out drum. Drum coating or film starting to wear thin
Wiper Blade Failure
The next most common laser cartridge failure to occur would be due to an issue with the Wiper Blade. After the image is transferred from the Drum to paper or Drum to Transfer Belt there will be residual waste toner on the Drums surface which needs to be cleaned before the next revolution of the Drum. The Wiper Blades job is to collect/clean/scrap any residual waste toner from the Drums surface, depositing it into the waste toner hopper.
Thin line down the page:
This is caused by a cut or nick in the blade which fails to collect/clean/scrape toner from the drums surface
effectively leaving a lined mark down the print. This can also be attributed to a worn blade.
Grey page with toner visible on drum:
The Wiper Blade isn’t applying adequate pressure to the drum to successfully clean the residual toner from the drum, which then gets applied to the next revolution of print. This is often due to the Wiper Blade not being correctly fixed in place (not screwed down properly, incorrect sealing foam etc).
It can also be caused by and old wiper blade that has gone hard over time. The stiffened blade does not apply adequate pressure to the surface of the drum limiting the collecting/cleaning/scraping capability of residual toner. An indicator of an aged Polyeurethane Wiper Blade is a yellow tinge.
Poorly lubricated blade, seizing drum revolution:
The Wiper Blade constantly applies pressure to the Drum, if the blade is poorly lubricated will stick to the drum and travel in the same direction. Once the Blade has flipped it will apply immense pressure to the drum often seizing it completely or requiring a fair amount of force to turn. Generally this will be accompanied by a loud clicking noise from the printer, thankfully the printer has a clutch to prevent stripping of gears. You will see some compatible colour cartridges using Yellow toner as a lubricant, the Yellow toner tends to be finer/smoother and works quite well as a form of powdered lubricant.
Magnetic Roller Failure
The Magnetic Sleeve is a coated aluminium roller that transfers the toner from the supply chamber to the drum by use of magnetic attraction; to break it down the Mag Roller sleeve encases a Magnet in the same shape as the Mag Sleeve. There is an electrical contact at the end of the sleeve to which a charge is applied to amplify the magnetic attraction. The (generally) black conductive coating found on the Mag Sleeve is made of various conductive materials with the sole aim of carrying the toner. Most failures are usually due to scratches or excessive wear of the coating. Toner particles in general are abrasive, when combined with pressure from the doctor blade doctoring/pressing toner against the Mag Sleeve roller causes wear to the coating. Some cartridges use a Developer Roller in place of a Magnetic Roller, this piece will be covered in a separate fact sheet to come.
Light print:
A worn out magnetic roller is probably the main reason for a light printing cartridge to occur. There is a black conductive coating that wears off
the sleeve over time. If the coating on the Mag Roller were to wear thin or completely through, you would be able to visually sight the black conductive coating turn pale (wearing thin) or even revealing the under aluminium tubing. This type of failure will show up more on solid black areas and grey scales. Normal text wouldn’t normally reveal this type of issue.
White voids in the print:
This is caused by scratches or gouges in the coating of the Mag Sleeve. Normally one or two scratches wouldn’t pose a problem however the more scratches there are then the more potential voids there will be. This is especially true when the scratches are all in the same general location.
Light and dark banding across page:
This is caused by a bent or warped magnetic roller. This normally happens when a hub (especially the metal ones) is pressed into the sleeve at an angle. Metal hubs should be removed and replaced with a special press or with delicate care.
Intermittent printing:
A Mag Sleeve contact transfers charge from the printer to the conductive black coating on the surface of the Mag Sleeve. If the contact is bent out of shape, too much electrical grease applied or installed incorrectly it can print either light or blank pages (most often blank).
PCR (Primary Charge Roller)
The PCR is a roller which controls the charge being applied to the Drum Cylinder. Basically it places an initial uniform charge on the drum then towards the end of the cycle erases the residual charge once more applying a uniform charge. This leads into the next print cycle (each revolution of the drum is considered a ‘cycle’). Because of this dual role, there are some severe failures which can come from the PCR. Most of these failures will show up more in winter where the humidity is low rather than in summer when it is high (this is due to Static build up).
Ghosting:
Ghosting is commonly known as repetition of print already applied to the page (duplication). It is more commonly seen replicating dense print however can repeat all density levels depending on the severity of additional charge (the replicated print is produced in lower density almost producing a silhouette replication of the print, hence the descriptive term ‘Ghosting’). A ghosting issue in general is derived from a charge related problem. This can occur when the outer coating of the PCR is faulty (too much cleaning fluid) or too much conductive grease is applied to the PCR Clips/Housing.
A cut or hole in the PCR:
This results in a repetitive black mark at equal distance to the circumference of the roller. Sometimes these marks can short out across the Drum Cylinder creating excess charge across the drum attracting additional toner when produces a dark ‘band’ horizontally across the page. The markings and ‘bands’ will be repetitive in nature (7+ repetitions down the page).
Random dots across the page:
These can either be black dots, or white dots in black areas. This is caused by excess lubrication powder sticking to the PCR. These dots will be repetitive in nature depending on the circumference of the PCR (7+ repetitions down the page).
Vertical marks on print, generally found on the LHS or RHS of page:
If the cartridge is still fresh and markings appear on the print in a blob or smear like fashion, generally this means the PCR has been marked with conductive grease. Commonly it will be located on the LHS or RHS of print near the PCR Clip/Housing (accidental conductive grease application to PCR coating). If continual printing is done, the grease will smear and transfer to the Drum
effectively giving a poor print vertically in the smear zone.
The Developer Roller
A Developer Roller is a metal shaft covered in Silicon Rubber with a specially designed surface coating. Both the coating and Silicon Rubber help in storing and releasing electrical charge. The Dev Roller is much like a Magnetic Roller, as they both help in the transferral of toner from toner supply chamber (hopper) to the Drum. The main difference between the two is how they deal in attracting and repelling toner; a Magnetic Roller utilises Magnetic Charge, where as a Developer Roller utilises electrical charge to attract and repel. Magnetic based toner will use a magnetic roller, if the toner is charged then a developer roller is used.
Light Printing:
A worn or dirty Developer Rollers’ surface coating is often the issue for a light print to occur. The Coating wears off
over a period of time and can be accelerated from other factors, such as environment (heat), inadequate Doctor Blade pressure or incorrect/dirty surface coating material. This type of failure will show up more on solid black areas and grey scales. Normal text won’t easily reveal this type of issue unless severe. Essentially less toner is attracted to the Developer Roller than normal.
Dark or Excessive Print:
Dark or excessive print on the page can be due to incorrect cleaning products being applied to the Developer Roller. The surface coating is a fragile balance of components/materials to aid in attracting or repelling specific toners. This balance can be disturbed when cleaning products are applied, which strip or leave additives (residue) on the surface coating. Majority of cleaning materials (looking at you Iso) are too harsh and end up stripping some of the coating. This allows the Dev Roller to overcharge causing excess toner to be attracted – which leads to dark or excessive prints.
Repetitive coloured marks equal distance down the Print:
Repetitions measured at the same circumference as the Developer Roller (smaller circumference) will indicate the Dev Roller has been marked. This can occur from sudden force damaging the surface coating of the Developer Roller
Repetitive coloured horizontal lines equidistance down the Print:
Repetitive lines measured at the same circumference as the Developer Roller (smaller circumference) will indicate the Dev Roller has been marked. This generally occurs from gradual force from the Doctor Blade pressing into the Developer Roller eventually pitting the roller out of shape.
Brother TN3440 Toner Reset
HL-L6200 HL- L5000D HL-L5100 HL-L5200D HL-L5200DWT HL-L6200DW HL-6200DWT HL-6400DW
Sometimes cartridge is installed – not recognised or shows empty
This issue relates to the Flag Gear found on the cartridge
“Most Brother Laser cartridges have a “Reset Flag”
On the side of the cartridges there is a little flag gear, which is basically a lever. When the cartridge is inserted into the printer for the first time and the printer engine runs, all the gears will motion and will release the flag gear forward. This flag gear moves forward and hits a sensor inside the printer. The sensor resets the toner level on the printer and this is how the toner level is monitored, the level will reset and count down till empty with no way to check during the countdown.
There are two positions for the reset flag and that is the “Unused” and the “Used” position. The flag gear is a moving part there is the chance for it to be ill-timed, miss it’s mark or not function correctly. This can occur with OEM ( Original Equipment manufacturer) as well as compatible cartridges, Brother have put a function within the printer to manually reset the toner levels.”
To manually reset the toner levels if the Flag Gear fails to do so, is quite easy to perform
1) Install cartridge/s into drum
2) Leave door open or open door if cartridge is installed
3) Press Secure/ Print and Cancel buttons at the same time
4) Arrow down to select correct cartridge needing to be reset.
5) Press OK
6) States Cartridge has been excepted
7) Close Door
8) Toner should be reset to READY.